“Should we just knock it down and start again?” is regularly how a conversation with new clients begins. There’s no magic answer but this handy guide walks homeowners through the decision-making process.
“Should we just knock it down and start again?” is regularly how a conversation with new clients begins. There’s no magic answer but this handy guide walks homeowners through the decision-making process.
One of the hardest questions we’re asked by clients is, ‘Should we just knock it down and start again?’ Unsurprisingly, there is no single right answer. However there is a fairly linear process to follow to get to the best answer for a specific project.
First: Can you afford a new home?
Budget is the first thing we work through because often it provides a swift answer. Anyone embarking on either a possible renovation or a new build needs to honestly understand their budget. Then the follow-up question is, ‘Can I afford to build the new house I want on this block of land?
Everyone involved needs to be realistic about how much building a new home costs. In some cases, it becomes fairly obvious quite quickly that the ‘knock down’ option is out of reach financially. Clients may likely feel disheartened but it’s better to be disappointed before you start spending money.
Then the question becomes: ‘Do we retrofit what we have … or do nothing at all?’ At this point, the questions about ‘what and how’ follow. With the right advice, the process can unfold in a fairly straightforward way.
Counting the cost of carbon
There’s a cost in dollars but also a cost in carbon emissions. So some clients have the budget for a knock down and rebuild but depending on their outlook and values, they may be asking themselves a more nuanced question: ‘We can afford to start over, but should we?’
Carbon emissions associated with building are a big topic but in brief: the construction industry contributes a whopping 18% of Australia’s total annual carbon emissions. There’s embodied carbon—all the emissions associated with the stuff we build with and everything involved in mining or making and transporting it. There’s at least a tonne of CO2 released for every square metre of a new Australian home. The second part is operational carbon, which is the carbon emissions associated with running the building. Often this is mostly energy for heating and cooling. A rebuild is going to need some new materials and that comes with a carbon cost. But it will be a lot less than sending an old house to landfill and starting over from scratch.
Some people arrive at our practice with a strong preference to conserve resources and it’s no different with their home. They don’t want to throw away the good bones that could support a radically better, more comfortable, healthier house.
It’s not to say it’s always the right decision. I can think of several projects that started with a rebuild intent but needed to be rethought when our research showed that fixing a very defective building would cost a lot more than starting over (the project pictured below, PassivCourtyard, is one example).
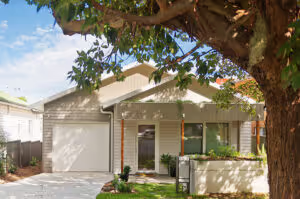
Increasingly, clients’ decisions are swayed by their awareness of the carbon footprint of a knock down rebuild. But if that is not a deciding factor, where to next in the process of making a decision?
Test your assumptions
Another project started as a knock down rebuild but we could see the good bones from the start and how this old double brick home perfectly occupied a site with a lot of constraints. We got as far as an initial design before we just had to draw the client’s attention to how much the new floor plan looked like the old floor plan.
That conversation came to a fairly swift conclusion with the clients saying to go ahead—if we could meet the design brief by retrofitting the current house for the same or less cost.
Next steps
Now we get to the crux of it. How did we determine this? First advantage: our practice had worked with this project’s builder before. Great: we love early involvement with experienced, capable contractors.
As part of designing the retrofit, we undertook energy modelling in the Passivhaus Planning Package (PHPP) software. This is how we work out exactly what would be required to bring this house up to scratch. The client wanted Passive House levels of performance so we modelled it to reach those targets. (EnerPHit is the official standard for retrofits, with certain targets being easier to achieve in recognition that it’s harder to fix what is already built.) We were investigating variables like the amount of insulation required, how we’d retrofit an air control layer and fit ventilation ducting and what type of glazing was needed. Just guessing is a really bad idea: it risks wasting client money and building uninhabitable hot boxes.
Accurately pinpointing the insulation sweetspot—not too much, not too little—is key with costing retrofits as it drives the construction details: how a wall or floor is built up, for instance. Costing the air control layer can be very tricky but we have enough experience that we are not groping about in the dark. On the basis of that modelling, we developed a simple scope of works in order to get a cost estimate. We were fortunate that our builder had been down this retrofit road before. We had a fair degree of confidence in his assumptions, mostly around the cost of labour.
Our experience building new Passivhaus homes in Sydney’s climate gave us certainty that the retrofit design would work. The scope document for the new build option was pretty similar in terms of construction details. We ignored the interior fitout. Because the two designs were similar in overall size, it was safe to assume that the kitchen, bathrooms and joinery were going to be a similar cost regardless.
The builder ran numbers on both options and it was near a dead heat. Based on the information we had at the time, the retrofit looked like it could be a tad cheaper. There was some contingency in the retrofit option to cushion the risk. We love that the client opted to fix what they had. The project is complete now and we love that the clients took the retrofit route. Let’s be clear, this was not a light touch renovation, it was a rebuild. But the results are fantastic. It finished ahead of schedule, on budget and smashed the performance targets. The blower door test (which measures how effective the air control layer is) came in at 0.46 ACHn50*, which meets the full Passivhaus target rather than the more lenient EnerPHit 1.0 ACHn50.
An honest closing observation about cost
For this project, ‘not more expensive than new’ got the retrofit over the line. We need to point out that there was an initial comparison of costs between rebuild and new build. But they are estimates. Because the new house wasn’t built, we don’t know exactly what it would have cost to build. So I can’t put my hand on my heart and say that without doubt the path we pursued was cheaper than the alternative. In reality, every bespoke project faces this challenge. You gather the best information you have, you make decision decisions taking into account hard data (thanks PHPP) and then you and the clients make decisions. At that point you make a commitment and move on it.
There’s no satisfaction or piece of mind to be had by continuing to wonder if the alternative would not have been cheaper, faster, or in some other way better. What we do know in this case, is the clients are really happy with their new old house.
*”Air changes per hour (ACH) is a measure of how many times an hour the entire volume of air within a house is replaced. For the sake of definition, it is expressed as ACHn 50, air changes per hour at 50 pascals. That is a measure of air pressure, equivalent to a moderately windy day”. —Passive House for New Zealand, a book by Jason Quinn.
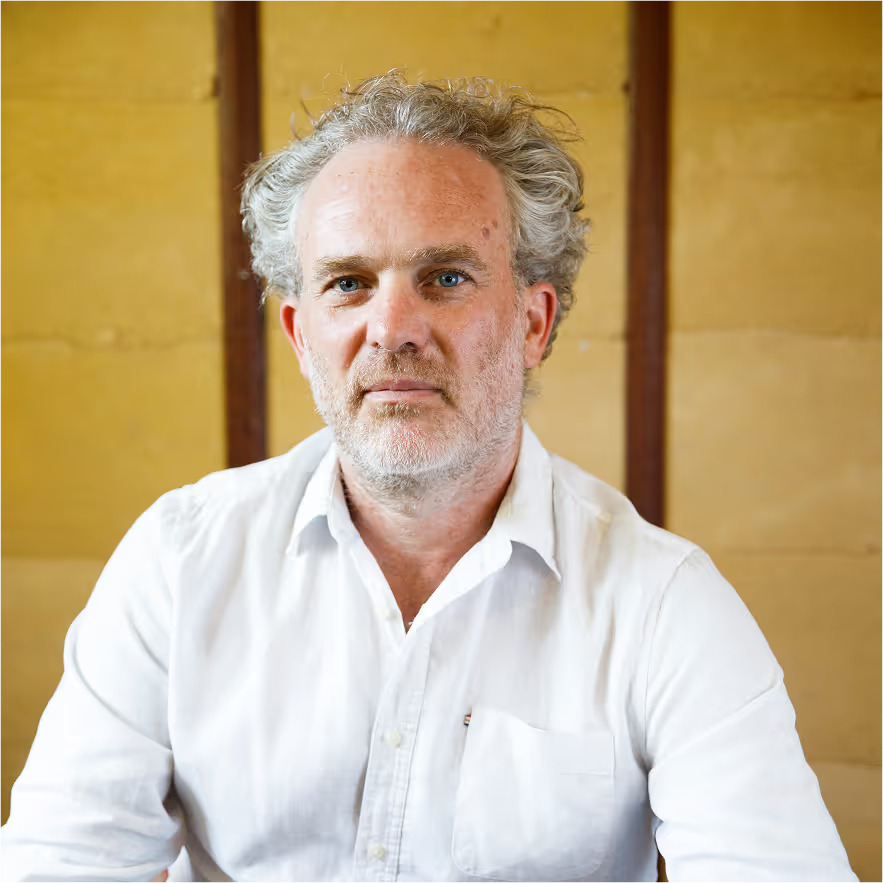
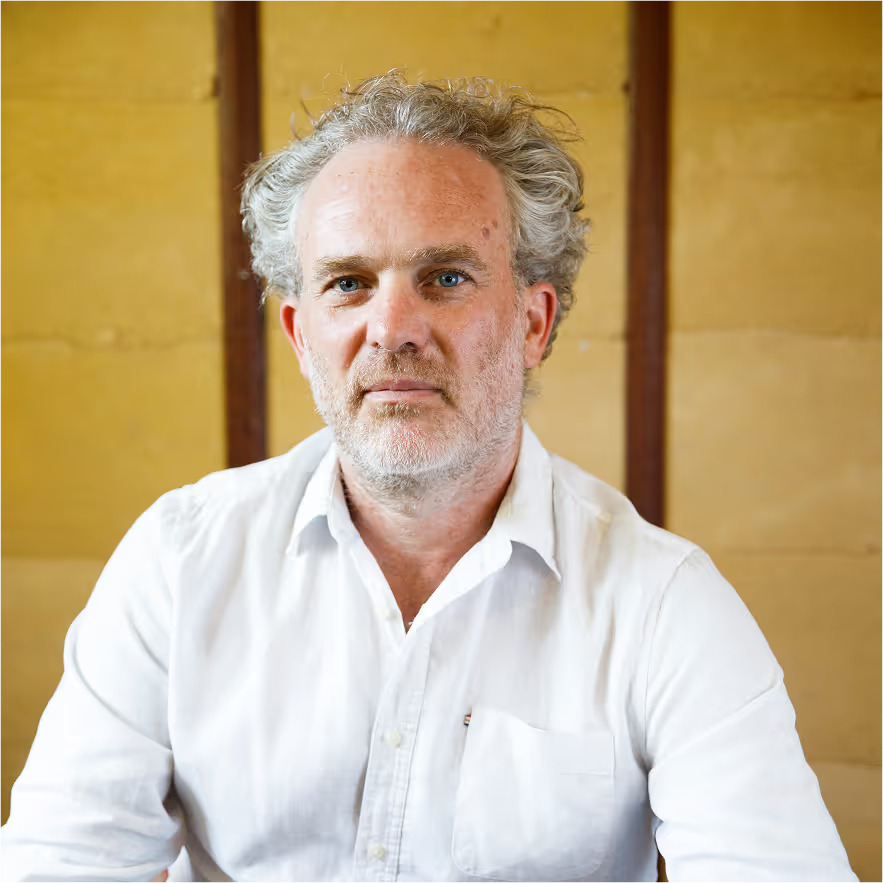
Andy joined Dick Clarke at Envirotecture as a young architect, gaining significant experience in designing genuinely sustainable buildings, both residential and non-residential, in Australia and overseas. After a stint at a large corporate practice, Andy returned to Envirotecture as a director in 2014. He went on to found Passivhaus Design & Construct in 2020, in order to make Passivhaus performance more accessible for more people.